Table of Content
As you finish a section, remove the pins and make sure the fabric of the shirt is not pleating beneath the neckband. Take the piece of fabric you cut for your neckband and sew the two short ends together using a straight stitch. Repeat the pinning process for the back of the shirt. Fold the t-shirt in half, but this time make sure the back of the shirt is on the outside.
"I want to make a few custom shirts. This was helpful to give me all of my options and how to do them in one place." Then, take a break to allow the bleach to react with the fabric of the shirt.Look over the shirt. If so, go back in with your bleach filled brush and even out the design. Remove the normal paper with the design from the contact paper as well. Using a hairdryer, apply even heat to the design for several minutes. Use very light pressure so you don’t push any ink through the screen.
Design T-Shirts Online
The letter and spacing should be in the correct way and interact with the graphics you’ve chosen. With the above step-by-step guide and tutorial, you can own a large collection of simple yet versatile T-shirts. If your T-shirt is loose, you can use a straight stitch.
The result is a different texture and looks from screen printing. Right from choosing the sewing fabric, cutting t-shirt pieces, and printing t-shirts at home, you will get a step by step tutorials. This process is a bit different because you must use dye sublimation-based ink and paper. With these types of designs, it’s best to print on white or lighter items made of 100% polyester. The printer we use for this is the Sawgrass Virtuoso SG500. Another cool way to create your custom tee is through the embroidery process.
Trending Articles
The easiest way to do this is to print the design and iron it onto a plain shirt. However, if you want to test the quality of your design, you can hire a printing company to create a professional prototype. Gluing a piece of lace or some other kind of ribbon onto the edges of a shirt’s collar or sleeves is another great way to embellish it. Cut the ribbon to the desired length, and then apply a thin layer of fabric glue where you want to attach the ribbon. Most custom ordering websites offer a wide range of shirts that you can design to your specifications. Choose the weight, neckline, and other special features that you want the shirt to have.
The process is straightforward and in just a few steps you’ll soon be wearing your own stylish designs. The method of using ink printed directly onto the fabric creates very soft prints but the downside is it will only give you the best results on very light fabric colors. This results in a highly durable and often times vivid print on light-colored fabrics. Just as with screen printing you will basically print your design color by color onto the transfer paper. The only difference is you will begin with the outer colors first, flash curing the plastisol ink before moving on to the next color.
Graphics & Digitizing Service
The wood should be of good quality so that you can have a sturdy frame that will keep the ink from spilling over to the rest of the t-shirt during printing. At this point you will want to refer to the paper manufacturer’s instructions for transferring the print. They will give you the ideal temperature settings and amount of time you will need to apply the heat. Screen printing is by far one of the most popular types of t-shirt printing and is also used to print on many other surfaces including posters, signage, and more. It is also known as silkscreen, serigraphy, and serigraph printing. Although there are certainly small manual screen printing setups one can use at home, it is most commonly used by professionals operating high volume print shops.

Take the pieces of your pattern and arrange them on your fabric according to your cutting instructions. Some pattern pieces will say "cut one on the fold," or "cut two on the fold." Line these pieces up along the fold of your fabric. Pinning the sleeves is a little different than pinning the front and back of the shirt. Flatten the sleeve on the paper and pin the seams.
Line it to one of the shoulders and pin it with the right sides facing inside in a way that will lay on the shoulder’s edge. With this, you will give half of your sleeve piece. Here’s a list of basic supplies you will need to begin your journey of how to make t-shirts at home. In this guide on how to make your own t-shirt, we will cover everything you need to know.
Place the coating tray at the bottom of the screen and carefully pour the emulsion on the screen as you move the tray up the screen. Make sure that the entire layout is internally consistent by keeping proportions reasonable, styles consistent, and colors cohesive. Determine the placement of the design on the t-shirt. Would your design work better as a centered image, an image on the top left of the t-shirt or as a wraparound image?
Begin cutting the design for each color and set them aside, you can also assemble the design to track your progress. Using your designs, you need to create a stencil for each color you intend to apply. This process is important and care should be taken to create accurate stencils. Start by running a test print using regular printing paper to see if everything looks good. Adjusting the printer settings to the best quality settings also helps to improve the overall print quality. If you're wondering what brand will give you quality results, take a quick look at 3DInsider's list of the best t-shirt transfer papers.
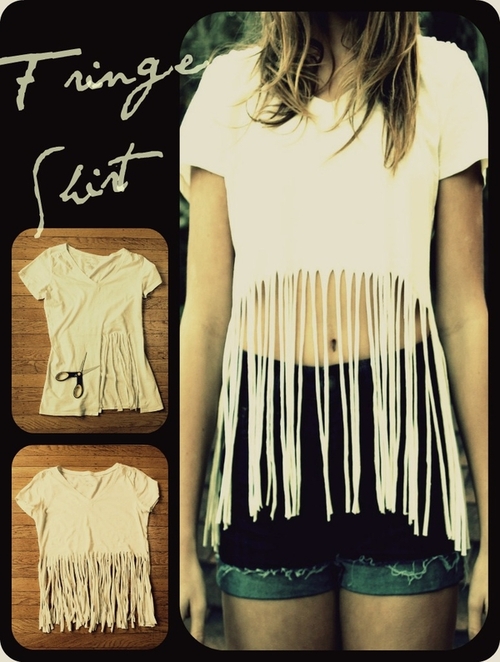
To make your own t-shirt, start by pinning a t-shirt that already fits you onto a piece of tracing paper. Then, trace your patterns for the front, back, sleeves, and neckband of the shirt, with ½ inch added around the outline for seam allowance. Next, pin your patterns onto the fabric, cut out your fabric pieces, and sew the shoulders together. Afterwards, sew the neckband to the neckline, and the sleeves to the arm holes. Finally, sew the side seams, starting from the end of the sleeve and working your way down the side of the shirt. The first factor used to calculate the cost of your order is the type of apparel and color you choose.
She lives a full, happy life in beautiful Ann Arbor, Michigan with her partner Greg, her teen daughter Alexa, and their two dogs, Hunter and Chloe. We offer 100% cotton short-sleeve crew neck T-shirts for adults and children. We only offer white color T-shirts at the moment. Print out your image onto transparency paper using a laser printer. This is what you will use to transfer the image to the screen. Make sure the image on your transparency mask is very opaque.
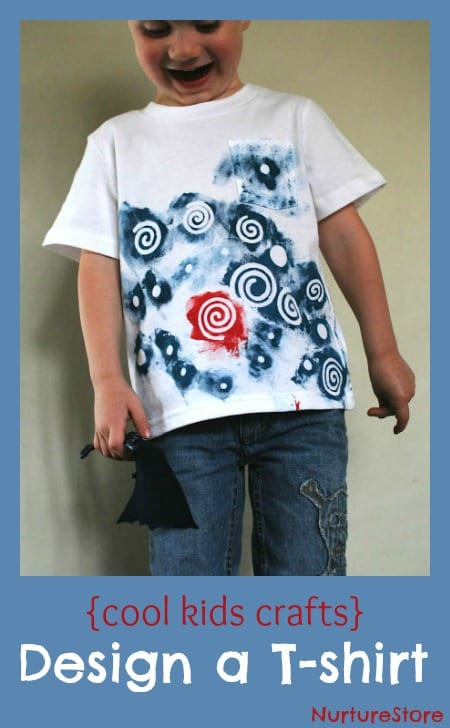
Mark Stephenson is the director of marketing at ColDes, a provider of customization equipment including UV printers, T-shirt printers, and embroidery machines. Mark is also a co-host of the Custom Apparel Startups Podcast. If you’re a home embroiderer now, you’re already on your way to understanding how to use the larger industrial machines. For example, the Avance 1501C embroidery machine has an updated touchscreen control panel like many of the pricier home machines do.
Use steady strokes to trace the chalk lines of your design. For an even bleach line, reload your brush every two inches. The fabric will quickly soak up the liquid so work quickly, but with a steady hand. Pour a few cups of the bleach into the glass or ceramic bowl. You don’t want any drops of bleach to end up on your clothing.

No comments:
Post a Comment